Experimental and numerical investigation of the vibration behavior of coupled blades
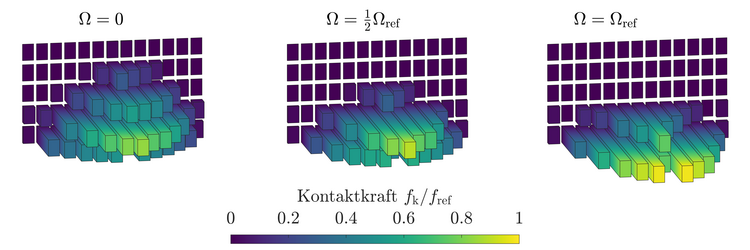
Led by: | Lars Panning-von Scheidt |
E-Mail: | jaeger@ids.uni-hannover.de |
Team: | Florian Jäger |
Year: | 2022 |
Funding: | AG Turbo |
Duration: | 01.09.2022-28.02.2026 |
Project describtion

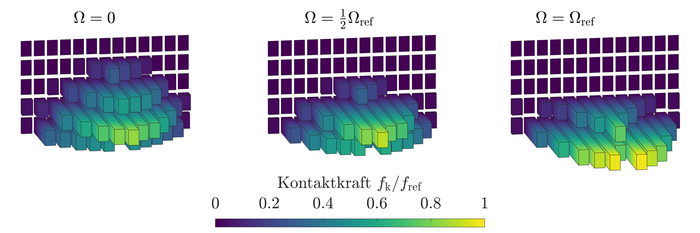
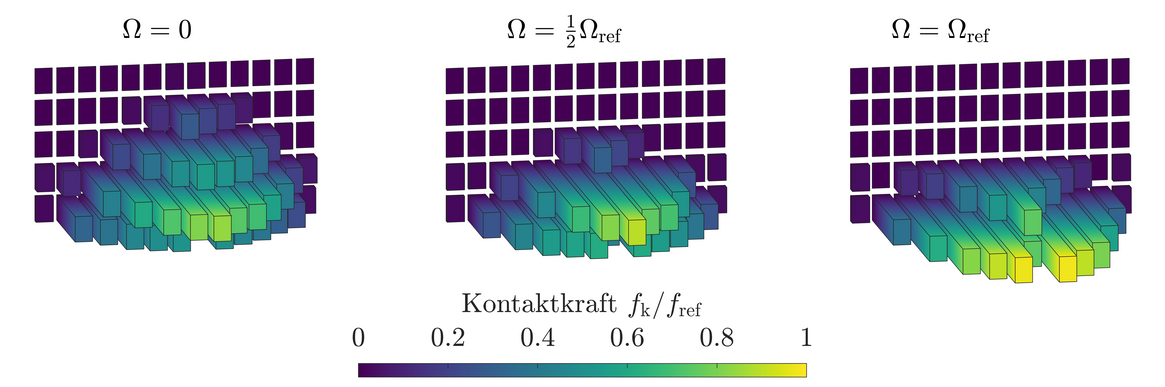
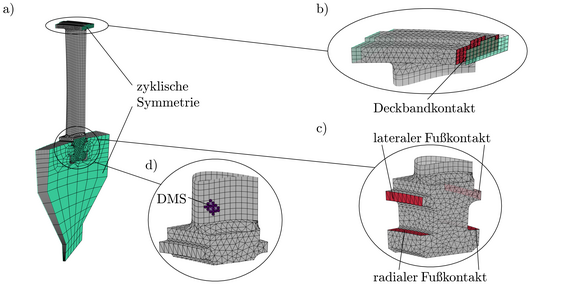
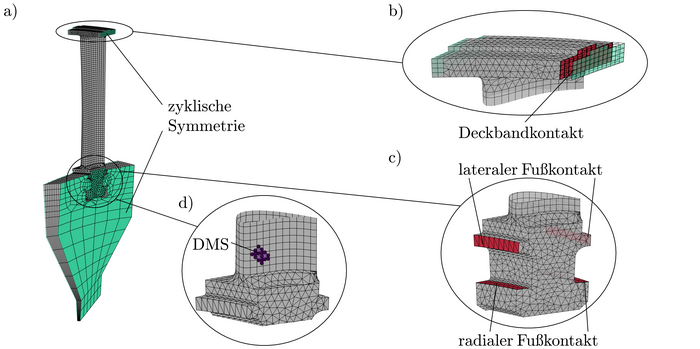
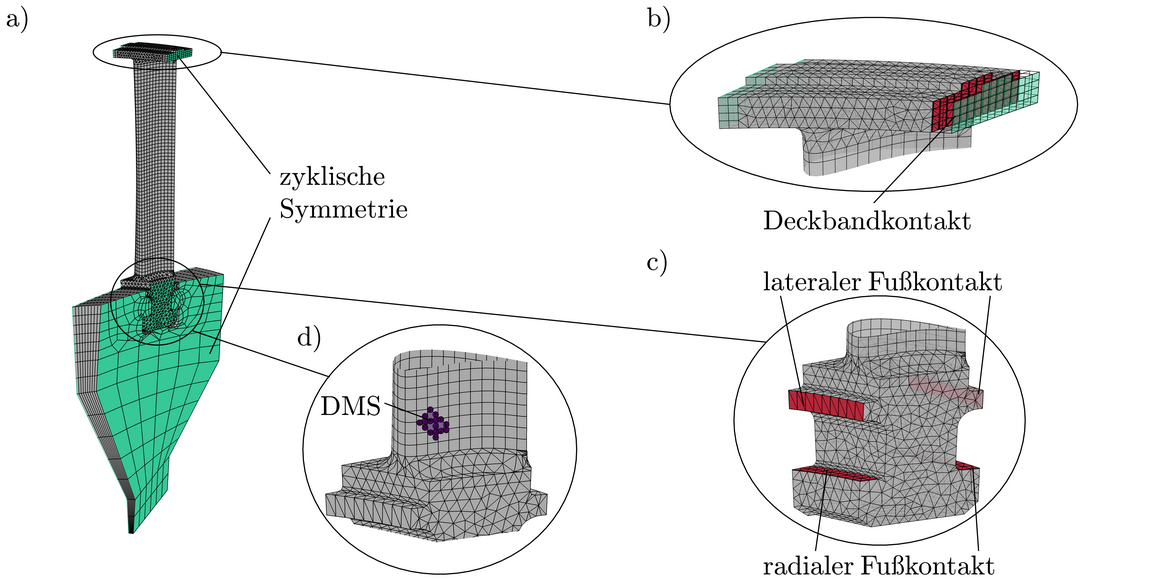

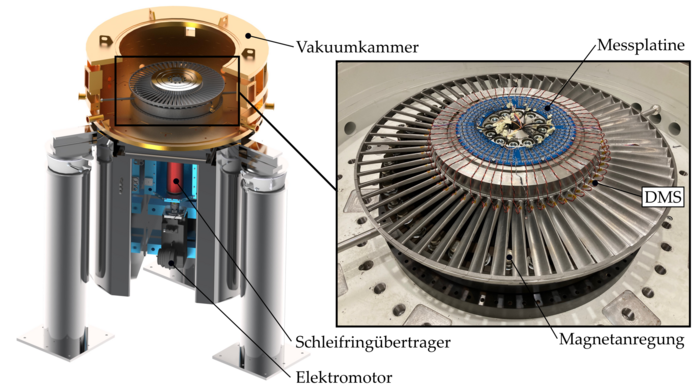
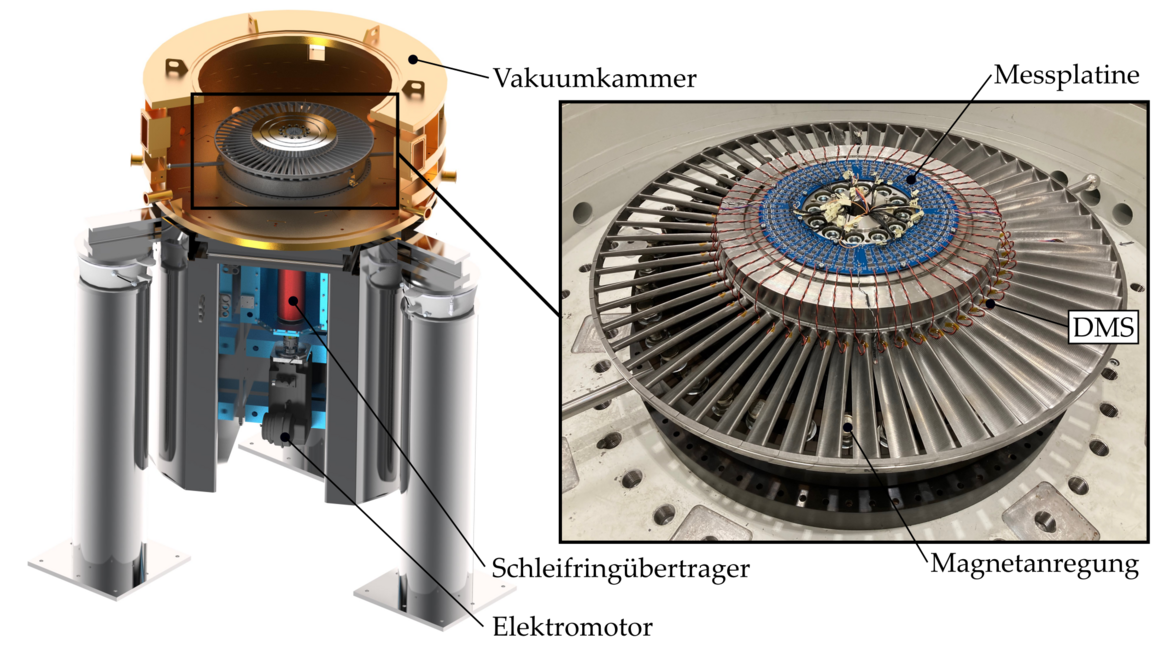
Turbine blades in turbomachinery are mechanically highly stressed components that can be excited to vibrate during operation. An established method for reducing vibration amplitudes is blade coupling via divided shrouds. The contact properties and thus also the damping efficiency depend significantly on a) the shroud oversize selected in the design process and b) the current operating point, see Figure 1.
In this project, the damping properties of turbine blades with shroud coupling are investigated experimentally and numerically. The modeling approach with an operating point variable reduction basis is being further developed for an efficient nonlinear frequency response computation. In the ROT2 rotational test rig at the IDS, tests are carried out at various operating speeds to experimentally validate the developed calculation program, see Figure 3.
Equidistantly distributed permanent magnets are used for excitation, whereby the excitation force level can be adjusted via the axial distance between the blading and the magnets. Strain gauges are used for the vibration measurement, and their signals are filtered and pre-amplified before being transmitted to the stationary measuring system via a slip ring transmitter. Excitation of the same vibration mode is achieved by varying the excitation order and using higher harmonic excitation force components. Figure 4 shows the results from the first measurement campaign and the corresponding simulation results.
In both graphs, the influence of the operating speed on the eigenfrequency and the damping properties is clearly recognizable. At the operating point with a higher rotational speed, a reduction in the eigenfrequency and a reduction in the vibration amplitude can be seen both in the experiment and in the simulation. This behavior results from the different contact preloads of the nonlinear friction contact on the shroud. At increased rotational speed, the blade expands in the radial direction, resulting in a change in the contact areas and forces. In the simulation, in addition to a qualitative adjustment, the frequency shift in particular could also be reproduced quantitatively. After a successful first measurement campaign, the shroud oversize is varied by grinding the shroud contacts on the individual blades and the tests at different operating speeds will be repeated.