Model-based Vibrational Analysis

Led by: | Lars Panning-von Scheidt |
E-Mail: | paehr@ids.uni-hannover.de |
Team: | Martin Paehr (Dynamics of Rotating Maschinery) |
Year: | 2023 |
Duration: | 01.07.2023-31.12.2025 |
Project Description
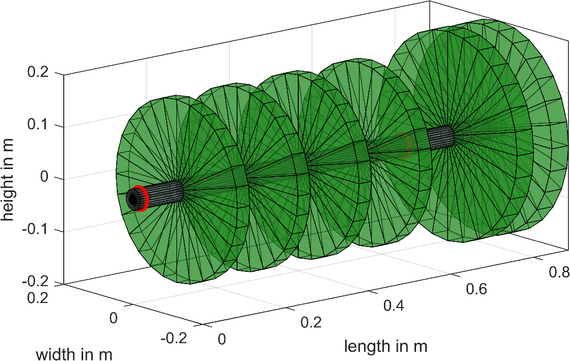
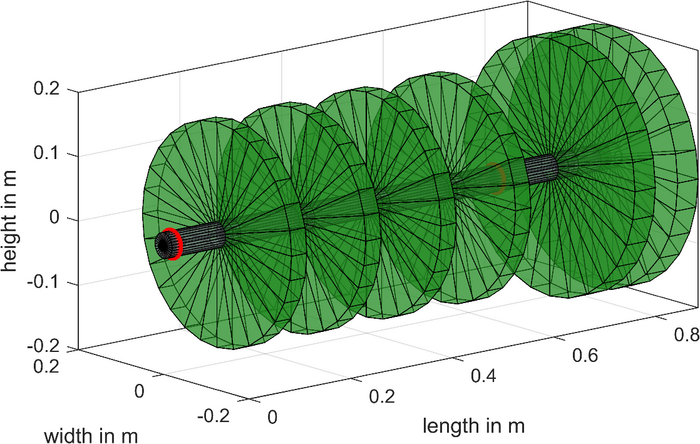

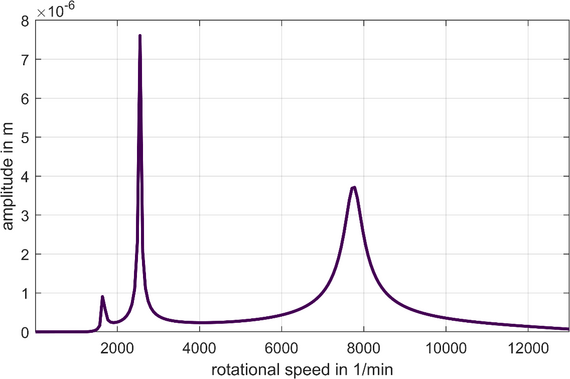
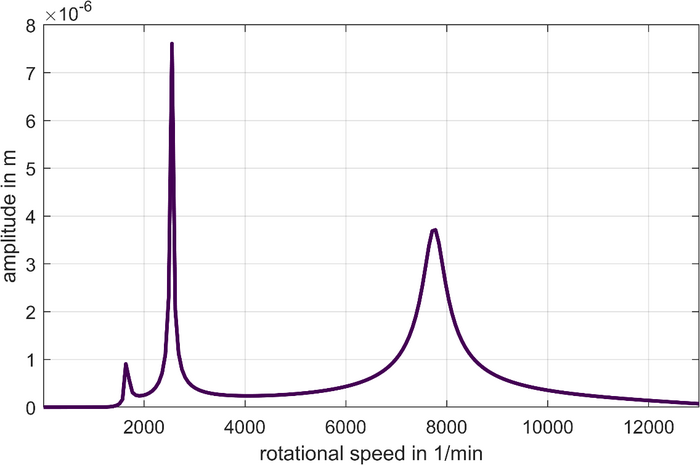
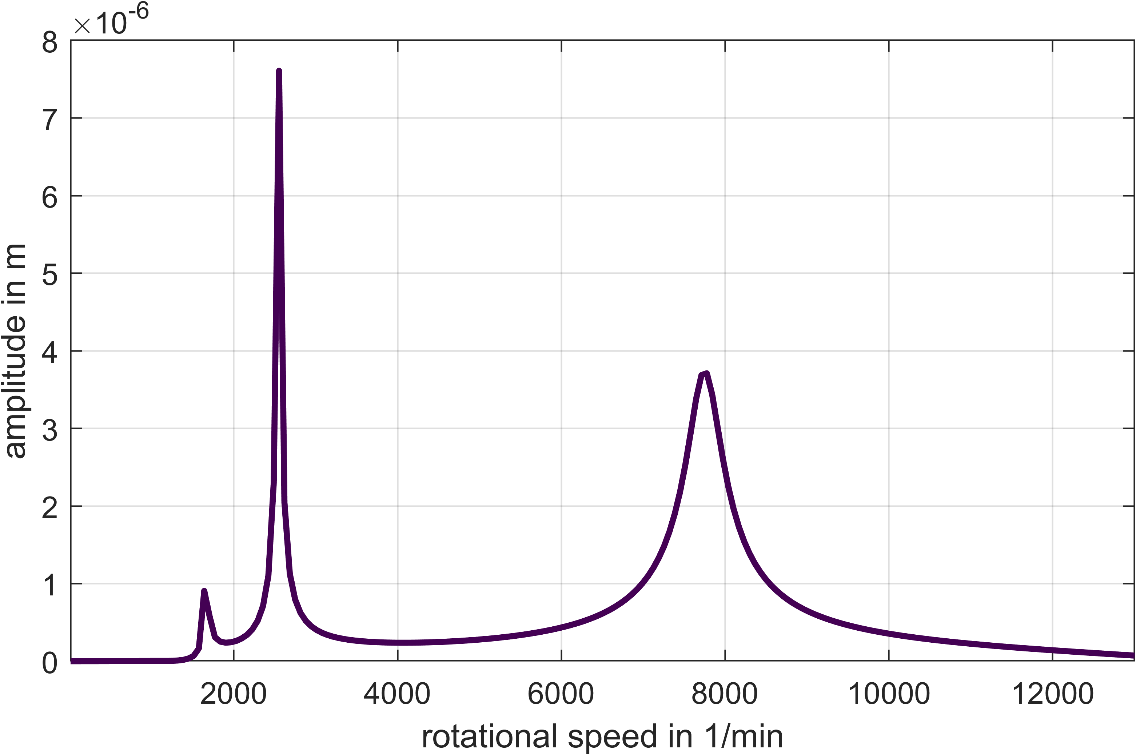
Aircraft engines are very complex power units whose operation is subject to many regulations. One of those regulations is a smooth operation with low vibrations, which is enforced by certain amplitude thresholds. Sometimes it can happen that those vibration limits are exceeded during the regular operation or during the engine tests that are part of maintenance. Often the troubleshooting is a very difficult and troublesome process which requires a lot of knowledge and thus can only be done by experienced technicians. The reason for this is the large number of possible excitation mechanisms in combination with the limited amount of measured data that can be used for the identification of the cause. This is why this process must be complemented by systematic data analysis which includes an automated fault detection. At the Institute of Dynamics and Vibration Research an rotordynamics simulation environment is being created for the development of an analysis tool. The simulation environment allows to set up the structural dynamics of aircraft engines by shaft and casing models and to analyze these models.
In Figure 1 an example for a rotor is presented that can be used to model vibrational problems in rotating machinery. This project focuses on the modeling of unbalances which is a very common fault of rotors and at a later stage rubbing between rotor and casing will be added.
An unbalance response of the shown rotor is presented in Figure 2. Particularly critical are the resonance crossing when the rotational speed of the rotor matches one of its natural frequencies and the oscillation amplitude become very large. This simulated vibrational data can be used to develop the above listed diagnostic tools. Finally, the identification process will be applied to real jet engine data.